![[The_Cube] with IBC sump](https://completebiogas.com/sites/completebiogas.com/files/main-assembly-with-ibc.png)
[The_Cube], professional version (deep base, bottom drain), as it might be seen at your neighborhood fast food outlet. The IBC next to it will collect effluent until the biogas entrepreneur that is leasing it to the restaurant returns once every week or two to replace the full IBC with an empty one.
[Note: The majority of the images in this page are ‘clickable’, and thus can be seen in larger sizes. Try clicking on the image above, for example.]
As of early 2024, I have decided that [The_Cube] was a very useful experiment, and a failed design. The primary thing is that the design is fragile, given that the polysty is not protected; the digester can be destroyed with one good kick right through one of the walls. Beyond that, the design is too complex. That said, the experiments I undertook while working with [The_Cube] proved to me that the basic idea of a “poly panel” digester is sound and worth further exploration. To reduce the cost and complexity of the initial implementation of the “poly panel” idea ([The_Cube]), and to dramatically increase the durability of a new design, I am now working on a smaller, cheaper, stronger “poly panel” digester, mentioned here. If you wish to support my work, please consider a purchase of my book, or if [The_Cube] intrigues you, please consider the purchase of a set of plans.
[Click here for printable/sharable/emailable PDF of this page. As well, if you want a 3D interactive model of [The_Cube], click here.]
[The_Cube] is the first example of a family of what we call ‘poly-panel’ digesters. These are digesters that make use of some of the properties of rigid polystyrene foam insulation (the pink stuff).
To help you understand what that means, we should explain a few things:
Containers: Convenience vs. flexibility
The first thing to think about when designing a digester is the container. And some may ask: “Why not just use an existing container? Why not use a septic tank or a cistern or an IBC?”
Well, there are several reasons, actually: good ones. I won't go into too much detail, but I suggest you think about two questions.
- First, how do you put an agitation device in an IBC or some other closed container? (Short answer: With enormous difficulty, or more likely, not at all.)
- And second, how do you put superior (and air-tight) insulation on (and all around and under) an existing container? (My short answer: Probably with very limited success. I would not use fiberglass insulation, since it loses 50% or more of its insulating value when tested at normal levels of humidity. So rigid insulation is better, and yet in turn, rigid insulation is almost impossible to properly put around, on top, and under an existing container so that it does not leak warm air from cracks and gaps near the top, and pull cold replacement air into the bottom cracks and gaps.)
TH said this at the May 2017 Aurora, OR Build-It Biogas Workshop, as you can hear for yourself in at the very end of this video.
Our conclusion was that we needed to have a container that we could build, so we could put whatever we wanted in it (agitation, heat exchange, gas recirculation, instrumentation), and, if properly designed, make sure that it was well insulated.
In addition and not coincidentally, having a box that we build out of six panels means that we can build the individual panels, pack them together flat and as efficiently as possible, add the various other parts and pieces, and ship a kit that can be built on-site to produce a sophisticated, small-scale digester. [The_Cube], in other words, can be kitted and shipped. (Coolio, eh?)
Polysty welded to polysty
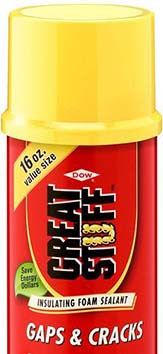
We started with a different design (the “press-plastic” digester, now little but a historical footnote), and in our research and experimentation, we did a substantial number of materials tests, trying to figure out how we could work with and ‘glue’ certain materials to other materials of interest: rigid polysty, polyethylene plastic sheets, wood, plywood, PVC sheets and pipes, and so on. One thing we found out which surprised us was that one bit of rigid polystyrene insulation can be welded to another bit by using sprayable urethane foam. (Here in the NW corner of the US, the most common version of sprayable urethane is “Great Stuff”.)
[But just a note here: ‘Great Stuff’ is terrible stuff. It sticks to everything, and when it gets on most things— like clothing— it is impossible to remove. Wear nice clothes when working with this ‘stuff’ and afterwards you won’t. Have nice clothes, I mean.]
The insulation is the container!
As soon as we saw that polystyrene could be welded to polystyrene, we realized that we could use it to make a welded box, one that could actually hold water, and maybe even be hermetic, “gas-tight”. And so we did make one. Several really. What we learned was that the promise of our experiments was borne out in practice: cut sheets of rigid polystyrene foam insulation can be welded together to make boxes (of many different sizes), and if those boxes are carefully made, they are hermetic.
(We usually want to be able to remove the top to check on the digester or fix something that may have gone wrong: so in this design, we do not weld the top in place. This means that one challenge is making a top that is not welded to the sides gas-tight, so the biogas won’t leak out; but it can be done.)
Dealing with the static pressure of water/slurry
What our experimental boxes also showed us, even when working with a welded polystyrene box that was only 18 inches high, was that the pressure of water in any box of a useful size was great enough that it caused the poly to be pushed out: the whole box wanted to ‘become spherical’. That, in turn, puts all the welds under tension, so they will crack and the box will leak or even fall apart completely.
The upshot is that the poly-only panels have to be supported with wood. (It doesn’t take much.)
Toxic? Degradable?
Those who understand biogas know how easily harmed the methanogens are. (These are the micro-beasties which actually produce the methane in biogas.) Those folks might wonder: Will polystyrene give off chemicals that harm anaerobic life? (After all, what's the point of having a neat-o new micro-beastie house if it poisons everyone who walks in the front door?)
[1] The… fluidized bed [digester] utilizes floatable particles… [as a ‘carrier’ or support for anaerobic biofilms in digesters using very watery or dilute slurries]. Synthetic materials are the most usual carriers in these studies, especially foamed polystyrene. [emphasis added.]
Garcia-Calderon, D., et al. “Anaerobic digestion of wine distillery wastewater in down-flow fluidized bed.” Water Research 32.12 (1998): 3593-3600. [link]
[2] “[The] degradation of wood under completely anaerobic conditions has not been unequivocally demonstrated.” [That is, over archeological time, i.e. many centuries, the biological destruction of wood which is underwater in completely anaerobic conditions is so rare that no one can prove it actually happens.]
Bowens, Amanda, ed. Underwater Archaeology: the NAS guide to principles and practices. John Wiley & Sons, 2011. [link]
Well, according to the literature (e.g. [1]), polysty beads have been used as an “inert” material in anaerobic digesters for better than 30 years. (That is, polysty does not harm the bitty beasties! The’ll really like their new home!)
Ok, fine: but what about the opposite problem? Will the polysty be attacked? Will it ‘biodegrade’ inside the digester? Will it get holes ‘eaten’ into it?
Well again, according to the literature, no, it won’t be degraded (or at least, not very much, not anaerobically, yada yada). After all, consider: there would be no reason to use polystyrene as an ‘inert carrier’ in your digester if it regularly disappeared: you want it to stay there and support your local biofilm, no? (And it does. Yet for those who want to know at least one way to deal with the polysty after the digester has served its time, see this article.)
So… Same questions about the wood, hey? Will the wood inside the digester get consumed like the organic materials fed in to produce the biogas? Well again, not enough to make any difference, according to the literature,[2] (or at least not for wood in truly anaerobic, zero free-oxygen environments, as contrasted with conditions that are merely ‘low-oxygen’).
Some parts of [The_Cube]
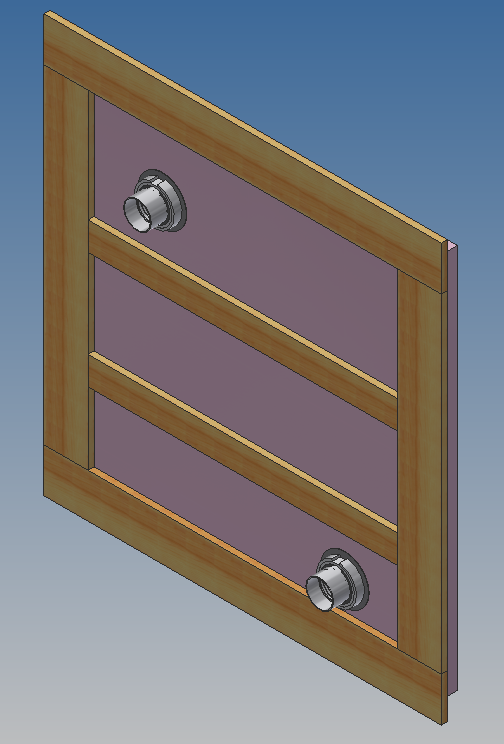
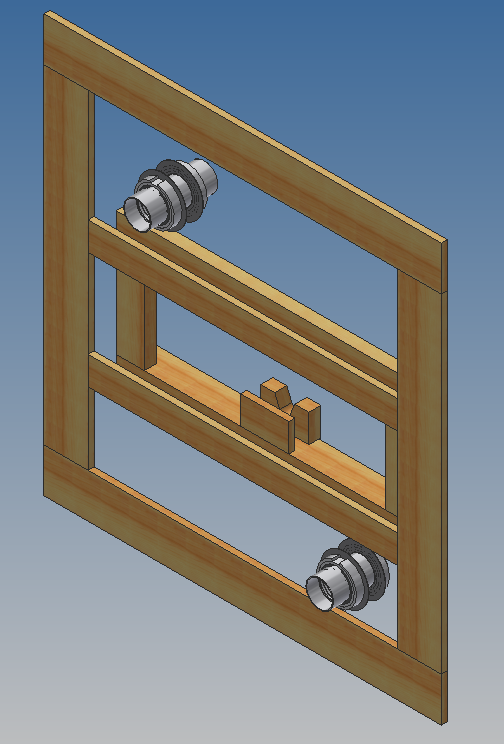
The front panel of [The_Cube], shown with the effluent pipe bung (top) and the drain bung (bottom). The image on the right is of that same panel with the polystyrene missing, showing the wood support inside.
“As for ‘waste disposal,’ we’ve got two mis-defined terms resulting in an abominable oxymoron. In nature there is no such thing as waste. All residues serve as resources for further growth— there is nothing to be disposed of. Nothing is thrown away. Indeed, there is no ‘away’. Everything must go somewhere.”
Bob Hamburg of Omega-Alpha Recycling Systems
Supported by wood, featuring bungs
To the left are two images of the front panel for [The_Cube]: the first shows the front panel with polysty, and the second shows the panel without polysty. You can see that the polystyrene is supported by wood support members. (These are screwed together, front to back, right through the polysty.) On the inside wooden framework in the image on the right we can also see the slotted piece that supports the axis for the agitator (click to see a larger picture; and there’s more about the agitator below). Also notice the ‘bungs’, those short pipes or holes in the poly panel. For any container, we need to put things in and get things out, and that means making holes in it. These bungs allow us to insert pipes into the poly panels and to seal around the pipes so that things don’t leak there either….
In sum, these are the three main items that make up any poly panel digester: polystyrene panels, wood supports, and bungs (more commonly called ‘bulkhead fittings’). (Want to know how to make such bungs? See this post.)
The Agitator
The inside of a digester, speaking biologically, is a very, very complex place. The materials fed into the digester go through many stages: breakdown into smaller particles and then into full liquefaction, followed by any of several different pathways breaking down complex chemicals into simpler and simpler chemicals. Each stage of this process is really accomplished by a different kind of life, as if, in this factory in reverse, we had the microlife from Noah’s Arc lined up along a disassembly line, or somewhat more accurately, along diverging disassembly lines.
So if you think about it you’ll see a rather strange thing: each group uses, as its food or energy source, what the preceding group left behind as its ‘waste products’. If the next group in line is missing for some reason, and therefore is unavailable to take the current group’s ‘waste’ and break it down to gain some of the energy stored in the chemical bonds, then the accumulation of ‘waste’ materials will tend to poison the current group. (Swimming in your own waste products, right?) So everyone has to be lined up, right there, cheek by jowl, ready to take whatever is left behind by those ahead in line, and to hand off whatever results from their disassembly to those next in line. It’s a biological bucket brigade, where the buckets start off filled with food waste, and by the end of the line, have almost nothing in them but liquid fertilizer, water, carbon dioxide and methane.
There’s a good deal more to the story, but the upshot for now is that we have to keep the contents of the digester stirred so that all those lovely biochemicals and astonishingly complex systems of anaerobic life are completely mixed together. What often happens in a digester that is not stirred is that the incoming slurry— the only slurry in most small digesters which is in motion— ‘short-circuits’ and takes the shortest path to the nearest exit. The remaining contents of the digester ‘go stale’ and stop producing methane.
Not having a way to stir up the contents a digester— not having the option of agitation, in other words— may well mean that your digester’s “effective volume”— the volume of slurry that is in active digestion— is some fraction of the actual volume.
The primary agitator for this digester is like an upside-down waterwheel. When enough biogas has been generated under one of what we call it’s “wings”, the buoyancy of the gas lifts and turns the agitator. So this agitator is intended to be self-powered.
The Gas Collection System
But will enough biogas be produced to cause the agitator to turn often enough to adequately stir the digester’s contents? I don’t know, as of December 2018…. In any case, it’s a more complicated question than it may at first appear.
Because we are still in a research and experimental phase with this digester design, we have added the ability to actively recirculate biogas into the digester: into the middle, to power the agitator, and into the corners to get more of the contents moving. We will be doing experiments, as time unfolds, to figure out how well the ideas work, and whether having gas recirculation is necessary or irrelevant— or something between.
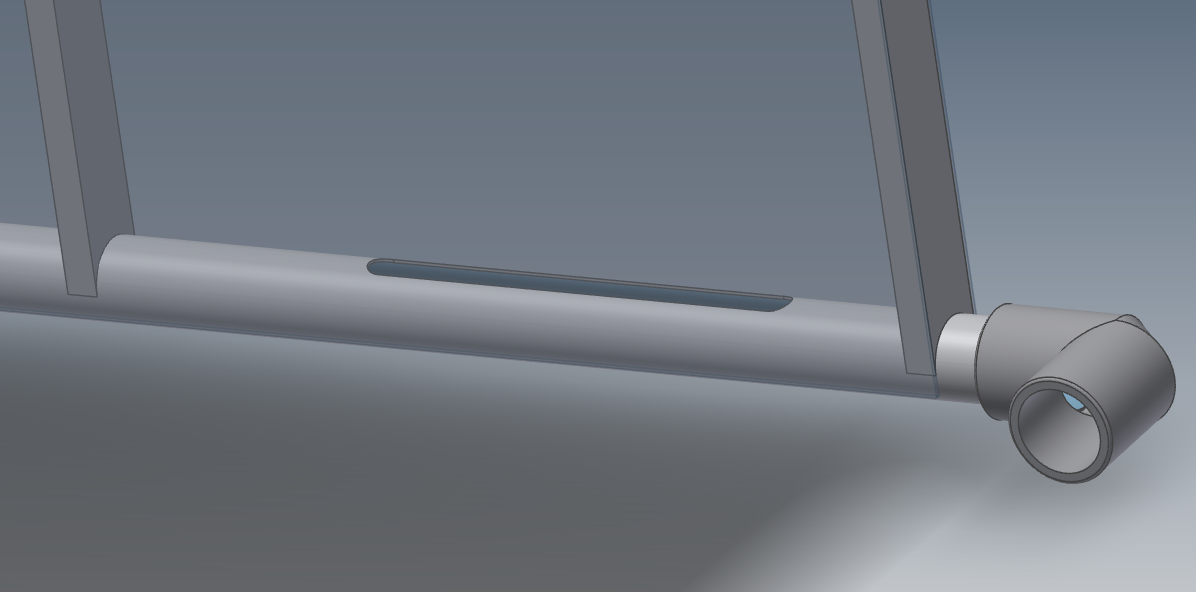
The PVC sheets in these images are rendered as semi-transparent. In practice, the sheets are opaque, and dark grey is the cheapest color.
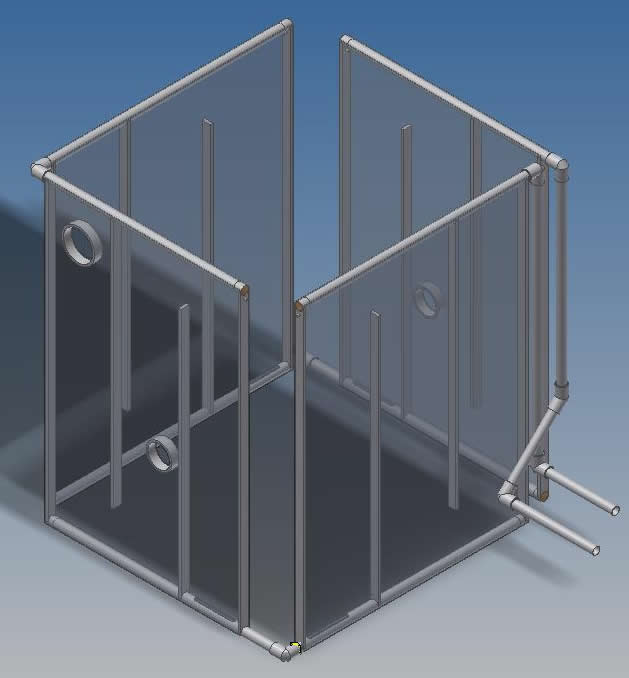
The Heat Exchange (HEx) units
We experimented with a number of different ways to pump heat into the digester. One of the most popular options for doing that is to run flexible pipe around the inside of the digester wall. I built and tried some alternatives using flex pipe, but I concluded after these experiments and my heat exchange calculations that it was not a great approach: too expensive. Too fussy. Too complex and time-consuming. Just... not elegant.
Meanwhile I had been working with PVC sheets to make the shields for my bungs, and one day I realized that I could glue a thin PVC sheet on either side of a slotted PVC pipe and run hot water through the pipe. The water would exit through the slot into the space between the two PVC sheets, and la voilá!: a heat exchanger.
According to my calculations, these HEx units are half the cost and twice the efficiency of a “ring around the digester” flex pipe solution that would take up about the same space.
(For an update on the evolution of the HEx unit design, see this post.
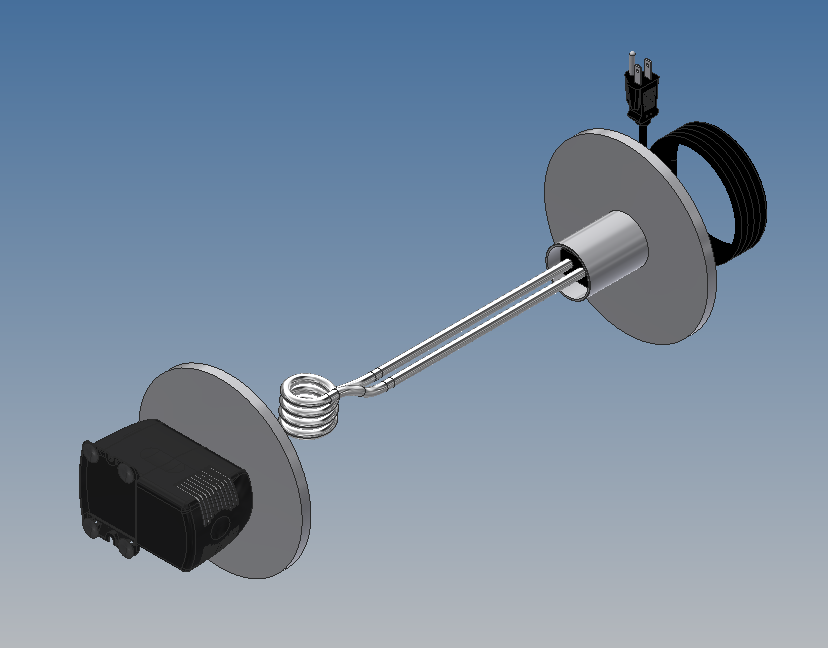
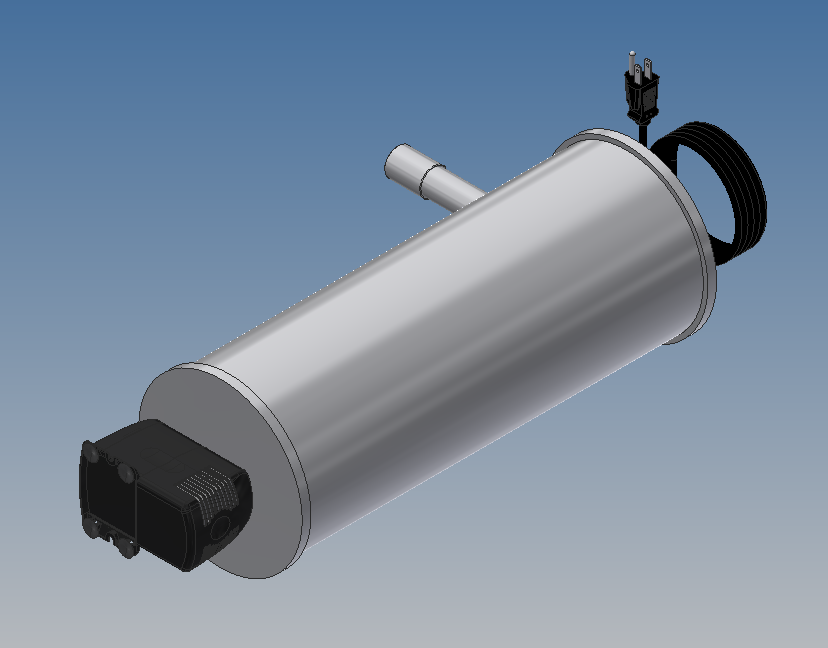
The heater core has a small, cheap ‘fountain’ pump on the right end, which is all that is required to push water through the HEx units.
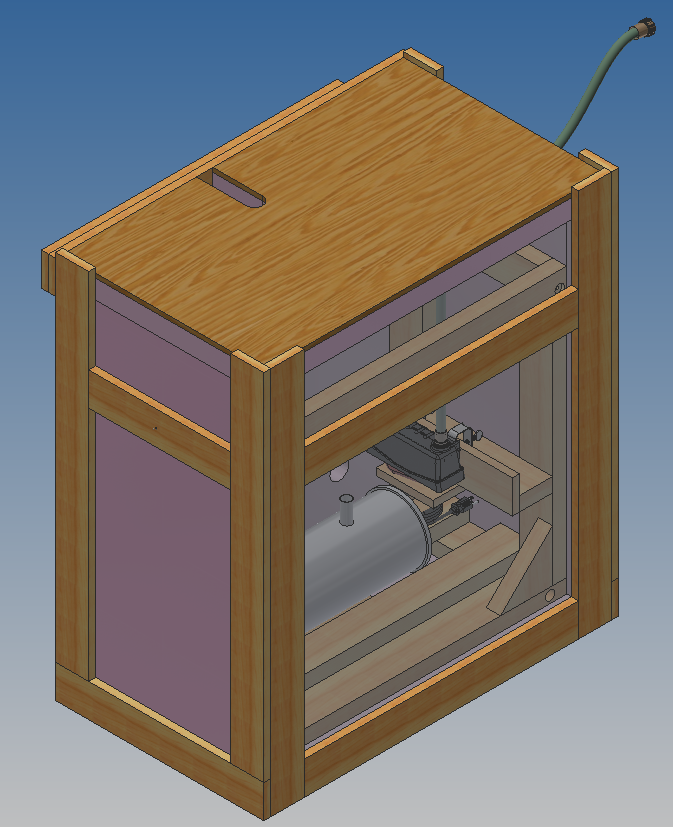
The hot water sump
At its present stage of development, the only heating option is electric. As the design matures, as further resources become available, as we have more and more of the million and one details (of the design and marketing and plans and calculations and learning new software and workshops) nailed down, then we will be working on solar and biogas heating options. (Hey, there’s just one of me, after all.)
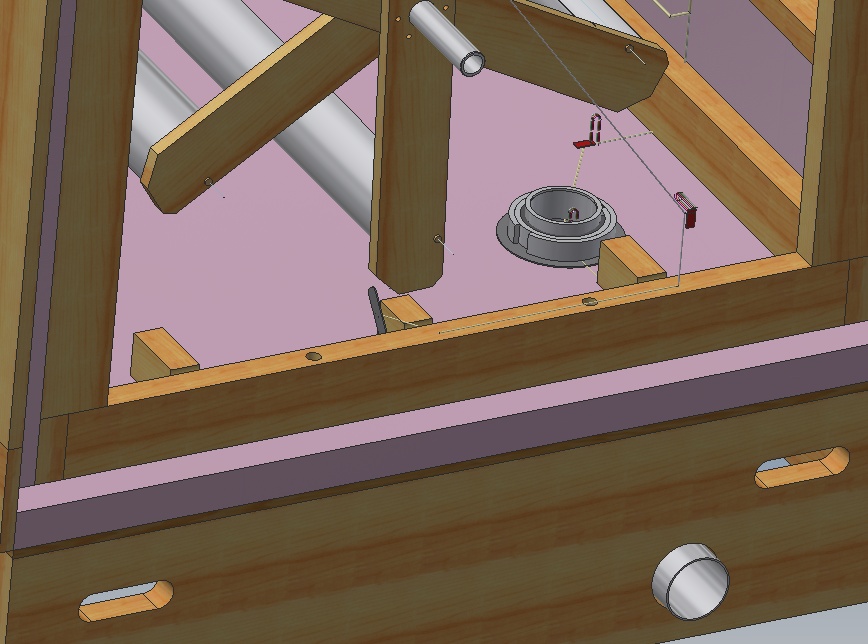
A reed switch, mounted on a piece of PVC sheet in the shape of a tongue depressor, offers a count of revolutions on the agitator. (As the unit rotates, a magnet embedded in one of its arms rotates around and closes the reed switch, one per full revolution.)
Instrumentation
Obviously there are more parts and aspects of [The_Cube] which we might discuss, but this page is already top-heavy, and prolix, and this is a world with limits. But it does seem important to mention instrumentation: those units that offer counts and measures to be collected and aggregated. The key point about instrumentation amounts to a philosophy of design with regard to digesters and many other things: “What we do not measure, we cannot improve.”
Consider: These digesters might be used in many ways, but to have the greatest impact, they must be used in applications where the numbers are important. How can an installer say to a restaurateur, “These digesters can help your bottom line”, if she has no numbers to show? Any claim of function or benefit, of outcome or production, must surely be likewise supported by the numbers.
Again, there’s only one of me, and the implied effort promises to consume a great deal of someone’s time going forward. Regardless of obstacles or difficulties, I intend— gradually perhaps, but with determination— to get those numbers.
Meanwhile, would like to see it, every stick of wood and polysty bit, in it’s nearly-completed form? You’re in luck, then: We have created a 3D model of [The_Cube]. Because this model is huge, @ 17mB, however, we are not at present hosting the page on this site. But fear not! You can download a zip file with everything you need to use the model locally, from here.
In sum, these are the first kittable, shippable, insulated, heatable, agitated (not to mention DIY) small-scale anaerobic digesters of which we have heard, worldwide. Do you know of any others? (We know of several kit digesters that are unheated and essentially unheatable, but none that are agitated.)
And here's another big thing which makes these digesters absolutely unique: In our workshops, we will teach you how to make them from materials you can purchase from Home Depot, Lowes, and/or some other hardware store. Learn how to make them, and you will have in your hands and head and heart the means of making them yourself forever, without ever purchasing so much as a #10 nail from us, ever again.
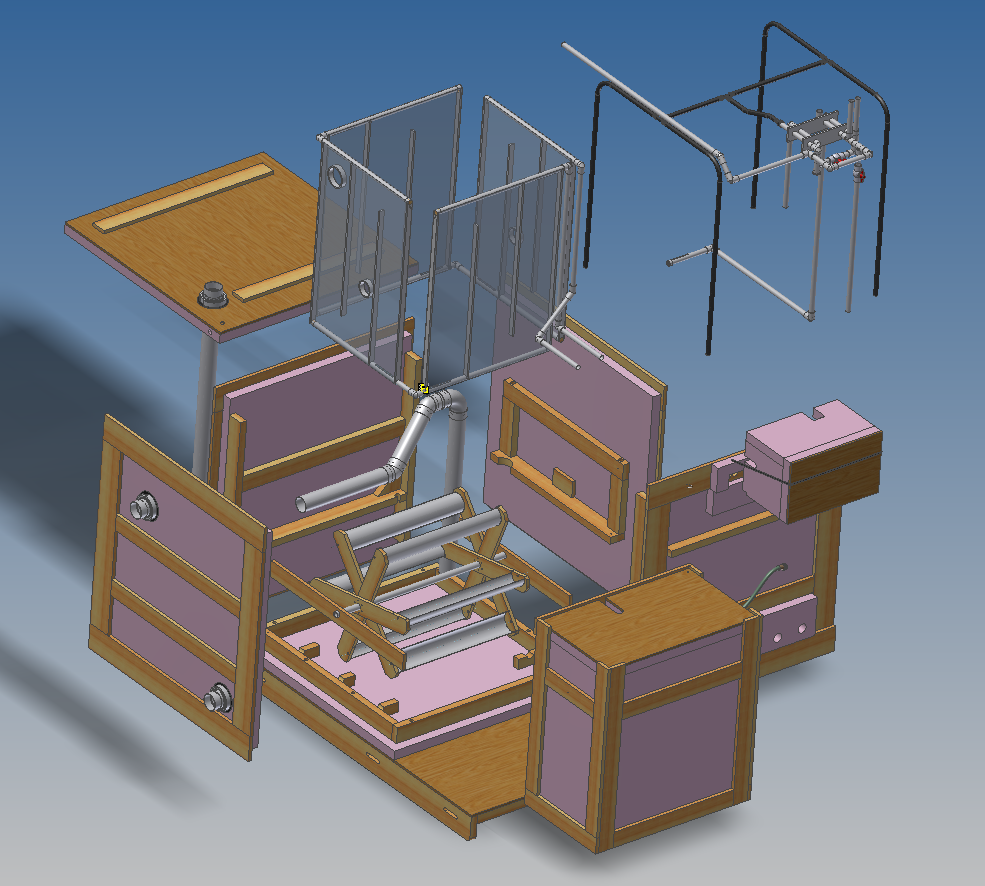